

The direction of the flow in the pump can also be changed by reversing the rotation of the pump. The fluid is then carried between the blades of the impeller and the casing, before being directed to and pushed out of the discharge. As the impeller rotates, the blades flex as they pass across the eccentric part of the casing, creating a vacuum to draw the fluid into the pump inlet. They use a rubber rotor (called an impeller, even though it isn’t) that has radially orientated blades. They can usually handle fluid temperatures from -32☌ to 260☌ and differential pressures to 15 bars (higher for hydraulic vane pumps).įlexible member pumps (also known as flexible vane or flexible impeller pumps) operate in a similar principle to vane pumps, except rather than sliding, the vanes flex. These pumps are known for being able to dry prime, easy to maintain, and having good suction characteristics. While they can be used with viscosities up to about 10,000 centipoise, efficiency drops quickly as it increases above 200 centipoise. Vane pumps are able to handle moderate viscosity fluids, with engineered non-metallic vane materials making these pumps well suited to handle low viscosity, non-lubricating liquids such as LP gas, ammonia, solvents, alcohol, fuel oils, gasoline, and refrigerants.Īs they have no internal metal-to-metal contact and self compensate for wear they can maintain peak performance when pumping these non-lubricating liquids. As the rotor continues around, the vanes sweep the fluid to the opposite side of the crescent where it is discharged through the discharge holes of the cam as the cavity volume decreases.As the rotation continues, the cavity volume increases, allowing fluid into the pumping chamber through holes in the cam.The tight seal among the vanes, rotor, cam, and side plate is key to the good suction characteristics common to the vane pumping principle. As the rotor rotates and fluid enters the pump, centrifugal force, hydraulic pressure, and/or pushrods push the vanes to the walls of the housing. Vanes or blades fit within the slots of the impeller. The rotor is sealed into the cam by two side plates. The rotor is located close to the wall of the cam so a crescent-shaped cavity is formed. A slotted rotor is eccentrically supported in an eccentric cam.Most vane pumps operate via the same general principle. Vane pumps are available in a number of vane configurations including sliding vane, flexible vane, swinging vane, rolling vane and external vane, with each type offering unique advantages.

They are typically classified based on the type of rotating element they utilise. Rotary pumps are commonly used for pumping high viscosity liquids such as oil including in handling lube oil and fuel oil in engine rooms.
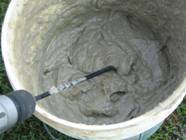
As they are designed to operate at relatively slow speeds to maintain these clearances, when operated at higher speeds they are susceptible to erosion and excessive wear which result in larger clearances and decreased pumping capacity. These pumps are designed with very small clearances between its rotating and stationary parts in order to minimise leakage from the discharge side to the suction side. These pumps are self-priming and provide near constant delivered capacity no matter the pressure. Rotary pumps are a type of positive displacement pump where for each revolution, a fixed volume of fluid is moved.
